Aluminum Casting Mastery: Methods and Devices for Extraordinary Results
Understanding the art of light weight aluminum spreading calls for a delicate balance of accuracy, technique, and the use of specialized tools. As we explore the intricate strategies and tools involved in light weight aluminum casting proficiency, one can not neglect the importance of sophisticated pouring and cooling down techniques that can boost the last end result.
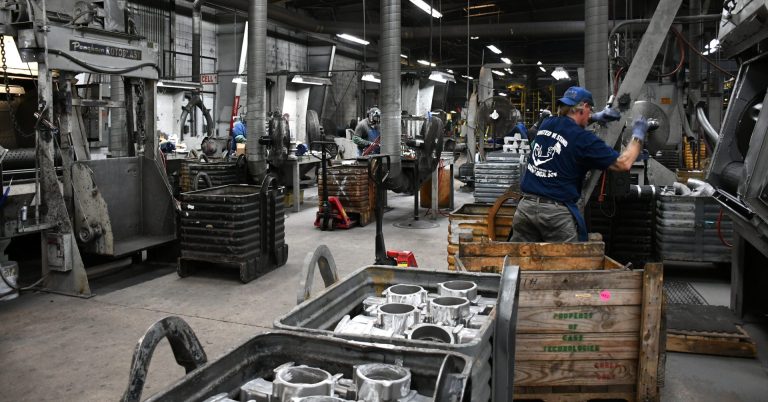
Value of Appropriate Melting Methods
Using precise temperature level control throughout the melting process is extremely important in ensuring the high quality and integrity of aluminum castings. The melting of light weight aluminum is an essential action in the spreading procedure, as it directly influences the last residential properties of the casted parts. Appropriate melting techniques are vital to achieve the wanted metallurgical framework, mechanical buildings, and surface coating of the light weight aluminum parts.
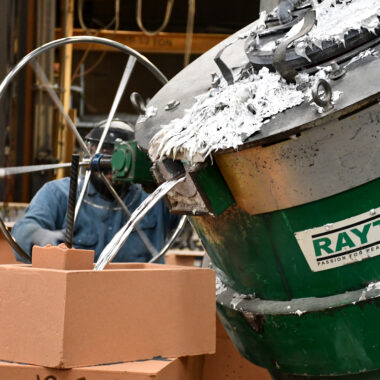
Moreover, tracking and changing the melt temperature level throughout the process aid prevent getting too hot, which can cause grain development and affect the general top quality of the light weight aluminum casting. Abiding by accurate melting strategies not only improves the top quality of the end product but also improves the efficiency and cost-effectiveness of the casting process.
Essential Mold Prep Work Steps
Appropriate preparation of molds is an essential facet in the aluminum casting process, making certain the successful replication of complex details and measurements in the final casted components. The vital mold and mildew prep work actions start with choosing the ideal molding product, such as sand or financial investment casting materials, based on the intricacy of the part and preferred surface. Before putting the molten aluminum, the mold and mildew tooth cavity must be thoroughly cleaned up and dried out to avoid flaws in the spreading. Additionally, using mold finishes can assist improve surface finish and prolong mold life.
Furthermore, appropriate gating and risering design are important in mold preparation to make certain audio spreadings with minimal issues like porosity and contraction. The gating system helps with the circulation of molten metal right into the mold cavity, while risers aid avoid shrinkage by giving added molten steel as the casting strengthens. Careful consideration of these facets during mold preparation dramatically contributes to the quality and honesty of the last light weight aluminum cast elements.
Advanced Pouring and Cooling Methods
Carrying out innovative pouring and cooling down methods is critical in maximizing the aluminum casting procedure for boosted effectiveness and high quality results. Utilizing methods such as vacuum cleaner spreading can dramatically minimize porosity in the final item, resulting in boosted mechanical homes. By leaving the air from the mold tooth cavity before putting, the threat of gas entrapment is minimized, leading to a denser and even more structurally sound casting.
Moreover, using regulated air conditioning approaches, such as water quenching or air cooling, can influence the product's microstructure and mechanical attributes (about aluminum casting). Rapid cooling can aid achieve better grain structures and boosted mechanical homes, making the actors light weight aluminum preferable for applications requiring high stamina and resilience
On top of that, carrying out directional solidification methods, where the casting solidifies progressively from one end to another, can help reduce inner problems and boost general component honesty. By very carefully handling the temperature level differentials during solidification, the formation of shrinkage porosity and warm rips can be reduced, bring about greater top quality spreadings with enhanced mechanical performance.
Crucial Tools for Light Weight Aluminum Spreading
Enhancing the efficiency and high quality end results of aluminum spreading processes counts greatly on the use of particular tools created to maximize different facets of the casting operation. One vital tool for light weight aluminum casting is the crucible. Crucibles are containers constructed from products like clay-graphite or silicon carbide that hold up against the high temperature levels needed for melting light weight aluminum. Crucibles are available in numerous dimensions to suit various casting volumes and are important for melting and putting the molten aluminum.
An additional vital tool is the mold. Mold and mildews can be made from products like plaster, metal, or sand and are used to shape the liquified aluminum right into the desired kind. about aluminum casting. click this link Appropriate mold and mildew layout and products are critical for accomplishing specific spreading measurements and surface finishes
Along with crucibles and mold and mildews, a heater is an essential device for light weight aluminum casting. Heaters heat up the steel to its melting point, guaranteeing it remains in a state all set for casting. Vital for keeping constant temperature levels and ensuring the light weight aluminum remains liquified, furnaces are readily available in different kinds, such as electric, gas, or induction heaters, each with its benefits for certain casting demands.
Completing Touches and High Quality Checks
Upon finishing the casting procedure, thorough focus to completing touches and extensive high quality checks is paramount to guarantee the integrity and precision of the aluminum elements - about aluminum casting. Ending up touches include the elimination of any excess product, such as flash, gating systems, or harsh edges, to achieve the preferred final shape and surface quality. This step frequently consists of procedures like grinding, fining sand, or fired blowing up to refine the appearance and appearance of the cast parts
Quality checks are after that carried out to confirm that the elements meet the specified demands and standards. These checks might involve dimensional inspections utilizing precision tools like calipers or coordinate measuring devices to guarantee accuracy. Additionally, non-destructive testing approaches such as ultrasonic testing or X-ray assessment can be used to detect any type of internal problems that might jeopardize the structural integrity of the parts.
Verdict
Finally, grasping aluminum casting strategies and using the right tools is necessary for achieving phenomenal results. Appropriate melting strategies, mold and mildew prep work, pouring and cooling approaches, along with completing touches and top quality checks are essential actions in the spreading procedure. By adhering to these steps meticulously and using the proper devices, one can guarantee a successful and high-grade light weight aluminum spreading manufacturing.
As we check out the elaborate strategies and devices involved in aluminum spreading mastery, one can not neglect the value of innovative pouring and cooling approaches that can visit this page elevate the final outcome.Correct preparation of molds is a fundamental element in the light weight aluminum spreading process, guaranteeing the successful duplication of elaborate details and dimensions in the last casted parts. Prior to pouring the molten aluminum, the mold dental caries need to be meticulously cleaned and dried out to prevent problems in the spreading.Enhancing the efficiency and quality results of light weight aluminum spreading procedures depends heavily on the use of particular devices made to enhance different elements of look at this site the casting operation.In enhancement to molds and crucibles, a furnace is an essential tool for aluminum spreading.